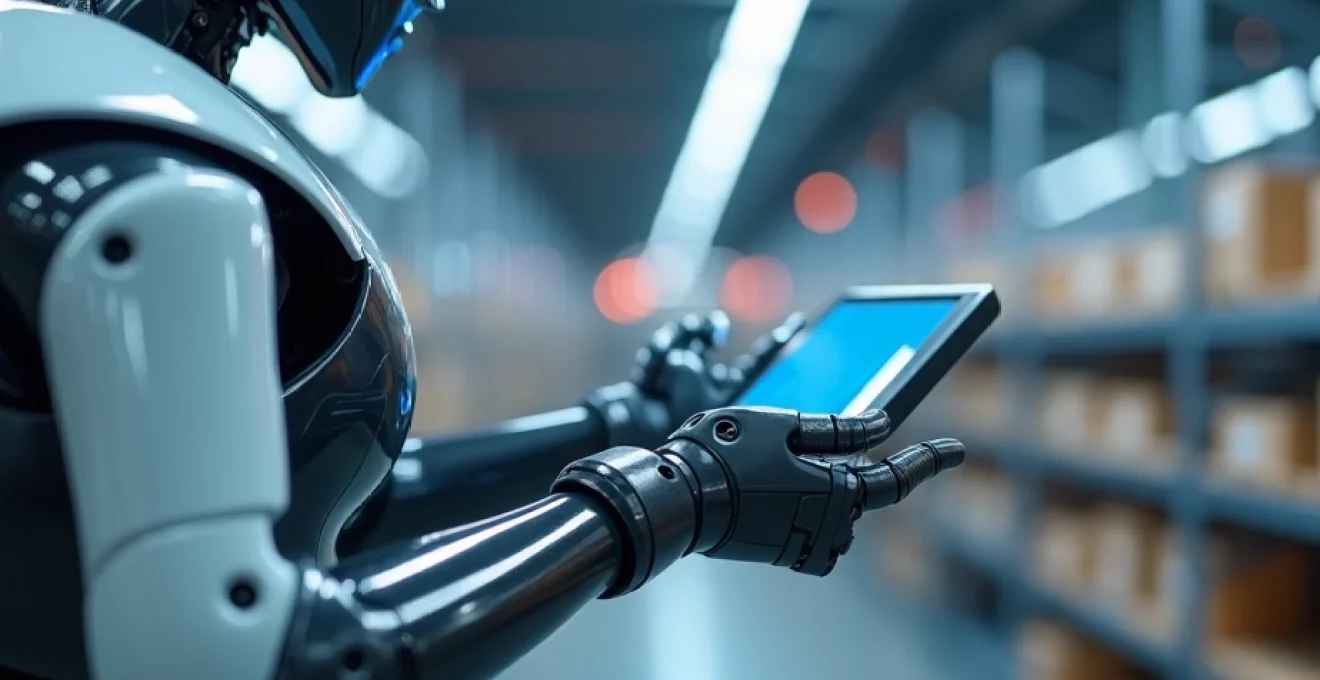
La robotica avanzata sta rivoluzionando il panorama industriale, portando significativi miglioramenti in termini di sicurezza e produttività. L’integrazione di sistemi robotici intelligenti e collaborativi sta trasformando radicalmente i processi produttivi, la logistica e la gestione della sicurezza sul lavoro. Queste tecnologie all’avanguardia non solo ottimizzano l’efficienza operativa, ma creano anche ambienti di lavoro più sicuri e ergonomici per gli operatori umani. Con l’evoluzione dell’Industria 4.0, la robotica avanzata si afferma come pilastro fondamentale per le aziende che mirano a rimanere competitive nel mercato globale, offrendo soluzioni innovative per affrontare le sfide della produzione moderna.
Evoluzione dei sistemi robotici nell’industria 4.0
L’Industria 4.0 ha segnato un punto di svolta nell’evoluzione dei sistemi robotici industriali. Le tecnologie emergenti come l’intelligenza artificiale, il machine learning e l’Internet of Things hanno potenziato le capacità dei robot, rendendoli più adattabili, intelligenti e interconnessi. I moderni sistemi robotici non sono più limitati a compiti ripetitivi e predefiniti, ma possono prendere decisioni autonome, adattarsi a cambiamenti dell’ambiente di lavoro e collaborare in modo sicuro con gli operatori umani.
L’integrazione di sensori avanzati e algoritmi di apprendimento automatico ha permesso ai robot di percepire l’ambiente circostante con un livello di dettaglio senza precedenti. Questa evoluzione ha aperto la strada a nuove applicazioni in settori come la produzione di precisione, la logistica automatizzata e la manutenzione predittiva. I robot di ultima generazione possono eseguire compiti complessi che in precedenza richiedevano l’intervento umano, migliorando sia la produttività che la qualità del prodotto finale.
Un aspetto cruciale di questa evoluzione è la crescente attenzione alla sicurezza e all’ergonomia. I moderni sistemi robotici sono progettati per operare in stretta prossimità con gli esseri umani, rispettando rigorosi standard di sicurezza. Questa coesistenza uomo-robot non solo aumenta l’efficienza produttiva, ma riduce anche il rischio di infortuni sul lavoro legati a compiti ripetitivi o pericolosi.
Implementazione di cobot collaborativi per la sicurezza sul lavoro
I robot collaborativi, o cobot, rappresentano una delle innovazioni più significative nel campo della robotica industriale. Questi sistemi sono progettati per lavorare a fianco degli operatori umani, combinando la precisione e la forza dei robot tradizionali con la flessibilità e l’intelligenza del lavoro umano. L’implementazione dei cobot ha un impatto positivo sulla sicurezza sul lavoro, riducendo il rischio di infortuni e migliorando l’ergonomia delle postazioni di lavoro.
Sensori avanzati e sistemi di visione artificiale nei cobot
I cobot sono equipaggiati con sensori avanzati e sistemi di visione artificiale che permettono loro di percepire l’ambiente circostante con estrema precisione. Questi sensori consentono ai robot di rilevare la presenza di operatori umani e di adattare il loro comportamento di conseguenza. Ad esempio, un cobot può rallentare o fermarsi completamente quando un lavoratore si avvicina troppo, garantendo la massima sicurezza durante le operazioni collaborative.
Algoritmi di apprendimento automatico per l’interazione uomo-robot
Gli algoritmi di apprendimento automatico giocano un ruolo fondamentale nell’ottimizzazione dell’interazione uomo-robot. Questi algoritmi permettono ai cobot di apprendere dalle esperienze passate e di adattarsi a nuove situazioni. Con il tempo, i robot collaborativi possono migliorare la loro capacità di anticipare i movimenti degli operatori umani, rendendo la collaborazione più fluida e sicura. Questa intelligenza adattiva riduce il rischio di collisioni accidentali e aumenta l’efficienza complessiva del processo produttivo.
Protocolli di sicurezza ISO/TS 15066 per robot collaborativi
L’implementazione dei cobot è regolata da rigorosi standard di sicurezza, in particolare dalla specifica tecnica ISO/TS 15066. Questo protocollo definisce i requisiti di sicurezza per i sistemi robotici collaborativi, inclusi i limiti di forza e velocità, le distanze di sicurezza e i metodi di valutazione del rischio. L’aderenza a questi standard garantisce che i cobot possano operare in stretta prossimità con gli esseri umani senza compromettere la sicurezza sul lavoro.
Case study: cobot universal robots UR10e nella produzione automotive
Un esempio concreto dell’impatto positivo dei cobot sulla sicurezza e la produttività è l’implementazione del modello Universal Robots UR10e in un impianto di produzione automotive. Questo cobot è stato integrato in una linea di assemblaggio per eseguire compiti di sollevamento e posizionamento di componenti pesanti. L’introduzione del UR10e ha portato a una riduzione del 30% degli infortuni legati a sforzi ripetitivi e ha aumentato la produttività del 25%. Gli operatori umani, liberati da compiti fisicamente impegnativi, hanno potuto concentrarsi su attività a maggior valore aggiunto, migliorando la qualità complessiva del prodotto finale.
Robotica mobile autonoma per l’ottimizzazione logistica
La robotica mobile autonoma sta rivoluzionando il settore della logistica, offrendo soluzioni innovative per l’ottimizzazione dei flussi di materiali all’interno di magazzini e impianti produttivi. I robot mobili autonomi (AMR) e i veicoli a guida automatica (AGV) rappresentano la nuova frontiera dell’automazione logistica, migliorando l’efficienza operativa e riducendo i rischi per la sicurezza dei lavoratori.
Tecnologie SLAM per la navigazione in ambienti dinamici
Le tecnologie SLAM (Simultaneous Localization and Mapping) sono alla base della navigazione autonoma dei robot mobili. Questi sistemi permettono ai robot di creare mappe in tempo reale dell’ambiente circostante e di localizzarsi all’interno di esse. La tecnologia SLAM consente ai robot di navigare in modo sicuro ed efficiente anche in ambienti dinamici, evitando ostacoli e adattandosi a cambiamenti del layout. Questa flessibilità riduce il rischio di collisioni e aumenta la sicurezza per gli operatori umani che condividono lo spazio di lavoro con i robot mobili.
Sistemi di gestione flotte AMR con intelligenza artificiale
L’intelligenza artificiale gioca un ruolo cruciale nella gestione delle flotte di robot mobili autonomi. I sistemi di gestione flotte basati su AI ottimizzano i percorsi dei robot, coordinano le attività di più unità e gestiscono le priorità dei compiti in tempo reale. Questi sistemi intelligenti possono prevedere i flussi di lavoro, anticipare le congestioni e riallocare le risorse in modo dinamico, migliorando l’efficienza complessiva delle operazioni logistiche.
Integrazione di AGV e AMR con sistemi WMS e MES
L’integrazione dei robot mobili con i sistemi di gestione del magazzino (WMS) e i sistemi di esecuzione della produzione (MES) crea un ecosistema logistico interconnesso e altamente efficiente. Questa integrazione permette una gestione ottimizzata dei flussi di materiali, sincronizzando le attività dei robot con le esigenze produttive e di stoccaggio. La comunicazione in tempo reale tra i sistemi robotici e i software gestionali riduce i tempi di attesa, minimizza gli errori e aumenta la tracciabilità dei prodotti.
Analisi ROI: implementazione di robot mobili KUKA KMP 1500 in magazzino
Un’analisi del ritorno sull’investimento (ROI) condotta su un’implementazione di robot mobili KUKA KMP 1500 in un grande magazzino ha mostrato risultati significativi. L’introduzione di una flotta di 10 robot KMP 1500 ha portato a un aumento del 40% nell’efficienza delle operazioni di prelievo e stoccaggio, riducendo al contempo gli incidenti legati alla movimentazione manuale dei materiali del 60%. Il ROI calcolato ha mostrato un periodo di ammortamento di soli 18 mesi, evidenziando il valore economico dell’automazione logistica avanzata.
Robotica di precisione per processi produttivi ad alta efficienza
La robotica di precisione sta trasformando i processi produttivi in numerosi settori industriali, consentendo livelli di accuratezza e ripetibilità prima inimmaginabili. Questi sistemi robotici avanzati non solo migliorano la qualità del prodotto finale, ma ottimizzano anche l’utilizzo delle risorse, riducendo gli sprechi e aumentando l’efficienza complessiva della produzione.
Sistemi di controllo adattivo e compensazione degli errori
I moderni robot di precisione sono dotati di sistemi di controllo adattivo che permettono loro di compensare in tempo reale eventuali deviazioni o errori. Questi sistemi utilizzano sensori ad alta risoluzione per monitorare costantemente i parametri di processo, come forze, temperature e vibrazioni. Grazie a algoritmi avanzati di compensazione , i robot possono adattare i loro movimenti con una precisione micrometrica, garantendo risultati consistenti anche in condizioni variabili.
Tecnologie di sensoristica avanzata per feedback in tempo reale
L’integrazione di sensori avanzati nei sistemi robotici di precisione fornisce un feedback in tempo reale sulle operazioni in corso. Sensori di forza, accelerometri e sistemi di visione ad alta risoluzione permettono ai robot di “sentire” e “vedere” con un livello di dettaglio senza precedenti. Questa capacità di percepire l’ambiente di lavoro con estrema precisione consente ai robot di eseguire compiti complessi come l’assemblaggio di componenti miniaturizzati o la lavorazione di materiali delicati con un margine di errore minimo.
Integrazione di sistemi robotici con tecnologie di stampa 3D industriale
La convergenza tra robotica di precisione e stampa 3D industriale sta aprendo nuove frontiere nella produzione additiva. I robot di precisione vengono utilizzati per guidare testine di stampa 3D con una precisione submillimetrica, consentendo la creazione di strutture complesse e personalizzate. Questa integrazione non solo migliora la qualità e la ripetibilità dei processi di stampa 3D, ma permette anche la realizzazione di componenti con geometrie prima impossibili da produrre con metodi tradizionali.
Cybersecurity e connettività sicura per sistemi robotici industriali
Con l’aumento della connettività e dell’intelligenza dei sistemi robotici industriali, la cybersecurity diventa un aspetto critico per garantire la sicurezza e l’integrità delle operazioni. La protezione dei robot industriali da attacchi informatici è fondamentale per prevenire interruzioni della produzione, furti di dati sensibili o potenziali rischi per la sicurezza fisica degli operatori.
Protocolli di comunicazione industriale sicuri: OPC UA e TSN
L’adozione di protocolli di comunicazione industriale sicuri come OPC UA (Open Platform Communications Unified Architecture) in combinazione con TSN (Time-Sensitive Networking) sta diventando lo standard de facto per la connettività sicura dei sistemi robotici. OPC UA offre un framework di comunicazione robusto e sicuro, mentre TSN garantisce la trasmissione deterministica dei dati in tempo reale. Questa combinazione assicura che le comunicazioni tra robot, controllori e sistemi di supervisione siano protette da intercettazioni e manipolazioni.
Implementazione di firewall industriali e segmentazione di rete
La sicurezza dei sistemi robotici richiede un approccio multi-livello che includa l’implementazione di firewall industriali specificamente progettati per proteggere le reti di automazione. La segmentazione della rete è una pratica essenziale per isolare i sistemi robotici critici dal resto dell’infrastruttura IT aziendale. Creando zone di sicurezza separate per i diversi componenti dell’ecosistema robotico, si riduce significativamente la superficie di attacco e si limita la potenziale propagazione di minacce informatiche.
Gestione delle vulnerabilità e aggiornamenti firmware per robot
La gestione proattiva delle vulnerabilità è cruciale per mantenere la sicurezza dei sistemi robotici nel tempo. Questo include la scansione regolare dei sistemi per identificare potenziali falle di sicurezza e l’applicazione tempestiva di patch e aggiornamenti firmware. Molti produttori di robot stanno adottando approcci di secure by design
, incorporando funzionalità di sicurezza direttamente nel firmware e fornendo meccanismi sicuri per gli aggiornamenti da remoto.
Analisi dei dati e manutenzione predittiva nei sistemi robotici
L’analisi avanzata dei dati e la manutenzione predittiva stanno trasformando la gestione dei sistemi robotici industriali, migliorando l’affidabilità, riducendo i tempi di inattività e ottimizzando le prestazioni complessive. L’integrazione di tecnologie IoT e algoritmi di machine learning permette di anticipare potenziali problemi e pianificare interventi di manutenzione in modo proattivo.
Implementazione di digital twin per simulazione e ottimizzazione
I digital twin, o gemelli digitali, rappresentano una replica virtuale dei sistemi robotici fisici. Questi modelli digitali dettagliati permettono di simulare e analizzare il comportamento dei robot in diverse condizioni operative, senza interferire con la produzione reale. L’implementazione di digital twin consente di ottimizzare i programmi di movimento, testare nuove configurazioni e identificare potenziali problemi prima che si verifichino nel mondo reale. Questa capacità di simulazione avanzata riduce i rischi associati all’implementazione di nuovi processi e migliora l’efficienza complessiva dei sistemi robotici.
Algoritmi di machine learning per previsione guasti e manutenzione
Gli algoritmi di machine learning stanno rivoluzionando l’approccio alla manutenzione dei sistemi robotici. Analizzando grandi volumi di dati operativi, questi algoritmi possono identificare anomalie nei dati operativi che potrebbero indicare un imminente guasto. Utilizzando tecniche di apprendimento automatico come l’analisi delle serie temporali e il rilevamento delle anomalie, è possibile prevedere quando un componente robotico potrebbe richiedere manutenzione o sostituzione. Questa manutenzione predittiva riduce significativamente i tempi di inattività non pianificati, aumenta la vita utile dei componenti e ottimizza i costi di manutenzione.
Integrazione di sistemi robotici con piattaforme IoT industriali
L’integrazione dei sistemi robotici con piattaforme IoT industriali crea un ecosistema connesso che permette il monitoraggio e l’ottimizzazione continua delle prestazioni. Le piattaforme IoT raccolgono dati in tempo reale da sensori distribuiti sui robot e nell’ambiente di produzione, creando un flusso costante di informazioni. Questi dati vengono poi elaborati e analizzati per fornire insights actionable sulla salute del sistema, l’efficienza operativa e le opportunità di miglioramento.
L’integrazione IoT facilita anche l’implementazione di strategie di manutenzione predittiva su larga scala. Ad esempio, una piattaforma IoT può aggregare dati da una flotta di robot distribuiti in più stabilimenti, identificando tendenze e modelli che potrebbero non essere evidenti osservando singole unità. Questo approccio olistico alla gestione dei sistemi robotici permette alle aziende di ottimizzare le prestazioni a livello di intera flotta, standardizzando le best practices e distribuendo gli aggiornamenti in modo coordinato.